УПОРСТВО И ТРУД ВСЕ ПЕРЕТРУТ25.01.2012
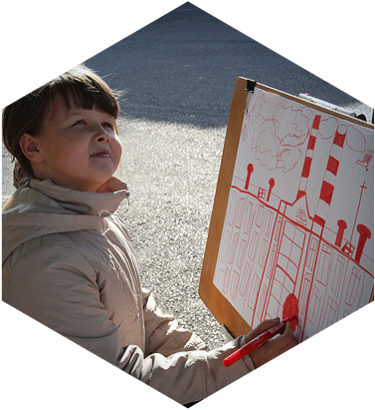
Исходя из сложившейся практики, окончательные итоги работы завода в 2011 году подведутся в течение первого квартала 2012 года. Тем не менее, главные результаты работы коллективов трех производств, которые упорно трудились по всем направлениям своей профессиональной деятельности и достигли определенных успехов, уже известны и работают по всем составляющим эффективной деятельности предприятия в целом.
Главный инвестиционный проект 2011 года - обеспечение ввода в эксплуатацию контактно-выпарного аппарата с внедрением собственного "ноу-хау" состоялся: в декабре произведен пуск установки в работу, результаты которой таковы, что в контактно-выпарном аппарате 46% раствор каустика упаривается до 63% концентрации гидроксида натрия.
Целью данной реконструкции явилось внедрение энергосберегающих "чистых" технологий с использованием в качестве теплоносителя продуктов сгорания водорода в кислороде, а так же увеличение выпуска твердого каустика с 35 до 50 тысяч тонн в год. В настоящий момент достигнуто увеличение выпуска твердого каустика со 100 до 158 тонн в сутки.
Во время остановочного капитального ремонта на 54 электролизерах нанесены диафрагмы. На текущий момент в аналогичном режиме работает половина электролизного парка. Проведена конкретная, объемная работа с иностранными компаниями по получению коммерческих предложений касающихся перевода существующих технологий по производству хлора на мембранную технологию, с соответствующим увеличением мощности.
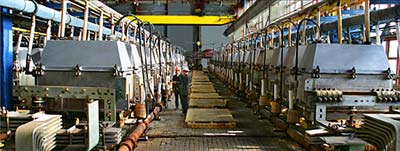
Зал диафрагменного электролиза
Обеспечивая надежность контроля опасных объектов, заменены изотопные уровнемеры на радарные уровнемеры на танках хранения жидкого хлора. Кроме того, смонтирована двухсекционная градирня ВГ-70 системы автономного водооборотного снабжения ртутного электролиза вместо прежней - физически изношенной. В феврале прошлого года успешно проведены испытания отечественного огнеупорного бетона, взамен импортного, в печи - реакторе по утилизации отходов, приведены в соответствие требованиям "Правил безопасности при производстве, хранении, транспортировании и применении хлора" ПБ 09-594-03 линии розлива жидкого хлора в баллоны, а также пущена в работу автоматическая система прогнозирования распространения хлора, произведена установка газоанализаторов в корпусе 132 в рамках проекта "Реконструкция системы локализации хлорной волны на установке хранения, испарения жидкого хлора".
К позитивным итогам 2011 года можно отнести работы в цехе получения кабельных пластикатов и пленок ПВХ по проведению опытно-промышленной наработки марки О-40 рец. ОМ-40 (черный) на линии гранулирования L01 с использованием новой металлосодержащей смазки "ОлеолК", разработанной специалистами инженерно- производственного центра (ИПЦ), что позволило улучшить технологические характеристики данной марки и увеличить производительность линий гранулирования.
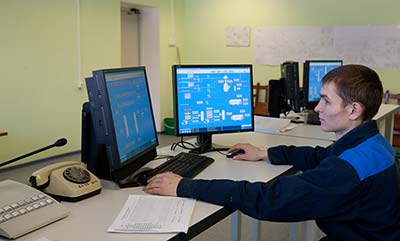
Операторная
Снижение себестоимости продукции - важное направление работы коллектива. В данном аспекте совместно со специалистами ИПЦ и ОЗС и ВМ предприняты меры по расширению сырьевой базы производства кабельного ПВХ пластиката и ленты ПВХ липкой. Проведены опытно-промышленные испытания, разработаны и утверждены расходные нормы альтернативного сырья для производства кабельного ПВХ пластиката и ленты липкой: пластификаторов, стабилизаторов и добавок различных зарубежных и отечественных производителей. Кроме того это позволило повысить качество отдельных марок кабельного пластиката.
В рамках расширения марочного ассортимента успешно прошла опытно-промышленная наработка кабельного ПВХ пластиката пониженной горючести марок НГП-М-ПО 30-35 и НГП-М-ПИ 30-30 по рецептурам, разработанным в инженерном центре предприятия. Образцы переданы некоторым потребителям кабельного пластиката и получены положительные отзывы по качеству и характеристикам переработки данного пластиката.
В I квартале 2012 года планируется производство еще одной марки кабельного ПВХ пластиката пониженной горючести марки НГП-М-ПВ 28, предназначенного для изготовления внутреннего заполнения кабелей и проводов, работающих в диапазоне температур от - 30°С до +70°С и эксплуатирующихся в условиях, требующих повышенной пожаробезопасности.
Внедренные инновации в процессе получения ПВХ обеспечили радикальное улучшение экологической ситуации, повлияли на увеличение интенсивности технологических процессов, четкость выдерживания параметров и качество конечной продукции. В частности успешно реализован первый этап испытаний новых марок эмульгаторов, программа интенсификации процесса полимеризации на реакторах путём более эффективного использования площади поверхности теплообмена обратных конденсаторов винилхлорида, при этом режим полимеризации сократился более чем на час.
Успешные испытания новых эмульгаторов на стадии полимеризации ВХ и перевод производства на данные эмульгаторы позволит в ближайшее время снизить себестоимость поливинилхлорида без ущерба для качества.
Очень актуальна работа по снижению коррозии оборудования и трубопроводов, которая проведена совместно с ИПЦ. По ее итогам в корпусе 1319, в отделении полимеризации, смонтирован узел дозирования щелочного раствора в конденсатор винилхлорида. Узел прошел обкатку в разных режимах и пущен в эксплуатацию, а содержание хлоридов и железа в рецикловом винилхлориде существенно снизились.
В планах персонала производства ПВХ на 2012 год числятся такие модернизационные меры как дальнейшие испытания новых эмульгаторов и окончательный переход на них; завершение работ по программе интенсификации режимов полимеризации при получении ПВХ С-6669ПЖ и С-7059М; пуск в работу узла пеногашения на реакторах с целью увеличения пробега обратных конденсаторов и снижения потерь времени, связанного с чистками теплообменников; монтаж насоса на линии захоложенной воды для улучшения конденсации винилхлорида и снижения его потерь.
В производстве дихлорэтана и винилхлорида также успешно внедрены инвестиционные решения. К ним смело можно отнести монтаж и пуск в работу газоанализатора содержания этилена в абгазах газовой смеси после дохлоратор, автоматизированной станции непрерывного контроля загрязнений атмосферного воздуха. Теперь контроль ведется в он-лайн режиме с поступлением информации не только в операторную цеха получения дихлорэтана, но и в отдел мониторинга ГУ УГАК, находящийся в г.Уфе.
Значимым событием по увеличению производительности ВХ и снижению издержек явился пуск новой печи пиролиза дихлорэтана, проведенный летом 2011 года. Новая печь, в отличие от ее предшественницы, оснащена более совершенными горелками, которые позволяют точно подобрать режим работы печи и снизить потери тепловой энергии.
Совместно со специалистами ИПЦ ведется работа по совершенствованию технологии утилизации хлорорганических отходов. В 2011 году были реализованы следующие мероприятия: внедрена двухскрубберная схема абсорбции, позволившая увеличить концентрацию абгазной соляной кислоты до товарного качества; усовершенствованы форсунки, обеспечившие улучшение процесса сжигания твердых и жидких хлорорганических отходов.
Специалисты цеха совместно с ИПЦ оптимизировали работу узла хлорирования рециклового ДХЭ, модернизировали смесители на установке утилизации абгазов производства ХВ, обеспечив стабильную работу установки. Отметим, что проведена большая работа по повышению эффективности очистки сточных вод от меди, алюминия и железа, достигнуты хорошие результаты.
Основные направления и объекты для технического переоснащения и модернизации в 2012 году находятся в плоскости стратегических целей развития производств Хлора-ВХ-ПВХ, то есть наращиванием мощностей до 600 тыс.тонн в год. Предпроектные проработки (ППТР), которые выполнены в 2011 году с привлечением проектной организации ЗАО "Полихимсервис", будут продолжены. Отметим уже сделанные шаги по разработке нового узла утилизации твердых хлорорганических отходов, который в перспективе должен обеспечить увеличение объемов утилизации твердых отходов по усовершенствованной технологии. Учитывая высокую эффективность совместной работы со специалистами ИПЦ и опытно-промышленного участка в части совершенствования существующих и разработки новых технологий, есть все предпосылки для реализации запланированных на 2012 год инноваций.